CELO, global industrial fasteners and screw manufacturer
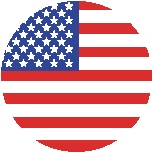
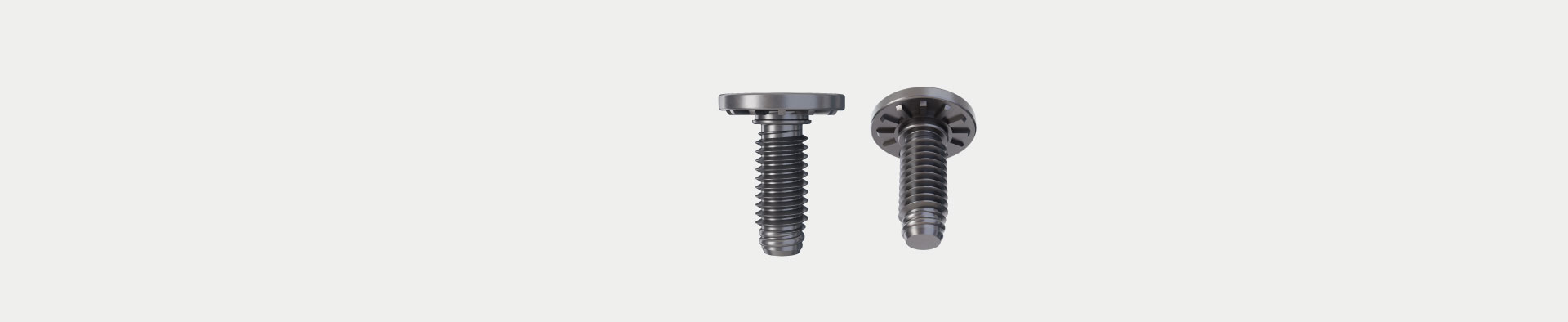
STRUX SM™
When to choose STRUX SM™ studs?
STRUX SM™ is a high-performance self-clinching stud designed to be staked in a pre-punched hole on soft metals and alloys, such as aluminum and copper. It offers a stronger and more reliable assembly alternative to traditional clinch and weld studs.
We recommend STRUX SM™ stud in the following situations:
- Applications that require consistent push-out and torsional resistance.
- Where welding dissimilar material is difficult or not possible.
How does STRUX SM™ stud work?
STRUX SM™ studs can be installed manually in-die or automatically with hydraulic staking presses or any equipment capable of feeding weld studs or conventional clinch studs.
For optimum performance, STRUX SM™ studs must be fully installed with no “gap” between stud and engaged material.
- The stud end is fed through a punched or drilled hole and into a lower die.
- A punch applies force to the stud and retaining ring passes through the pilot hole. As pressure is applied, the stress-distributing ribs are seated, forcing the engaged material into the retaining groove.
- Materials is displaced into the retaining groove. Stud is firmly locked into place.
STRUX SM™ studs benefits
- High push-out and rotation resistance during service. Exceptional torque-out performance in soft metals.
- Eliminates welding operations:
- No material damage due to excessive heat.
- Reduces the potential risk of corrosion.
- Improves the aesthetics of the end-product.
- Minimizes panel distortion. It allows STRUX SM™ stud to be installed closer together or closer to panel edge.
- Head diameter sized to prevent embedment of the stud into the application material.
- Fast and easy installation, adapted both to automatic feed and in-die installation.
- Cost saving opportunities:
- Eliminates the cost of additional components, as sealants to prevent leakage (or other elements required in the installation of alternative products).
- Eliminates production bottlenecks.
- Longer life of installation tooling when comparing to similar products.
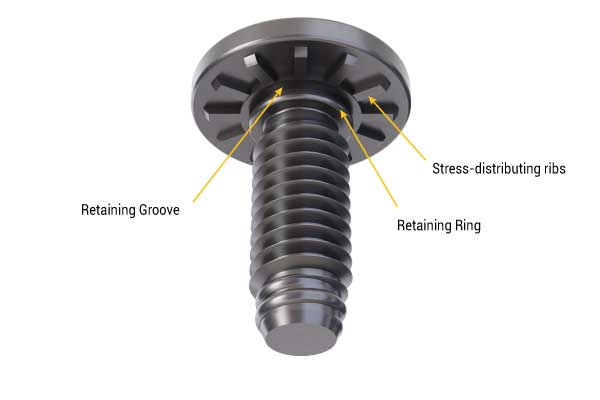
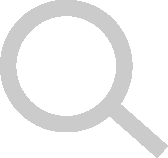
Screw design specifications
We produce STRUX SM™ studs on special demand to fit your exact requirements.
- We recommend to add MAThread® point to prevent cross-threading problem.
- Optical sorting is recommended to ensure a smooth nut assembly.
Recommended pilot hole size
Pilot hole for STRUX SM™ studs are designed according to a minimum material thickness. When installed in thicker materials, the results obtained are equal or with higher performance.
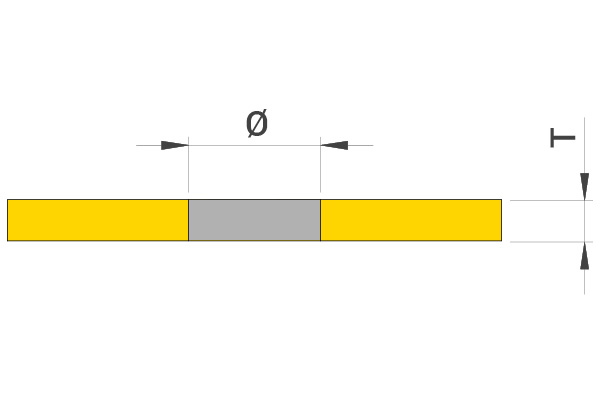
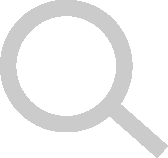